Table Saw Settlement Results in $2M Payment for Middle Finger Amputation
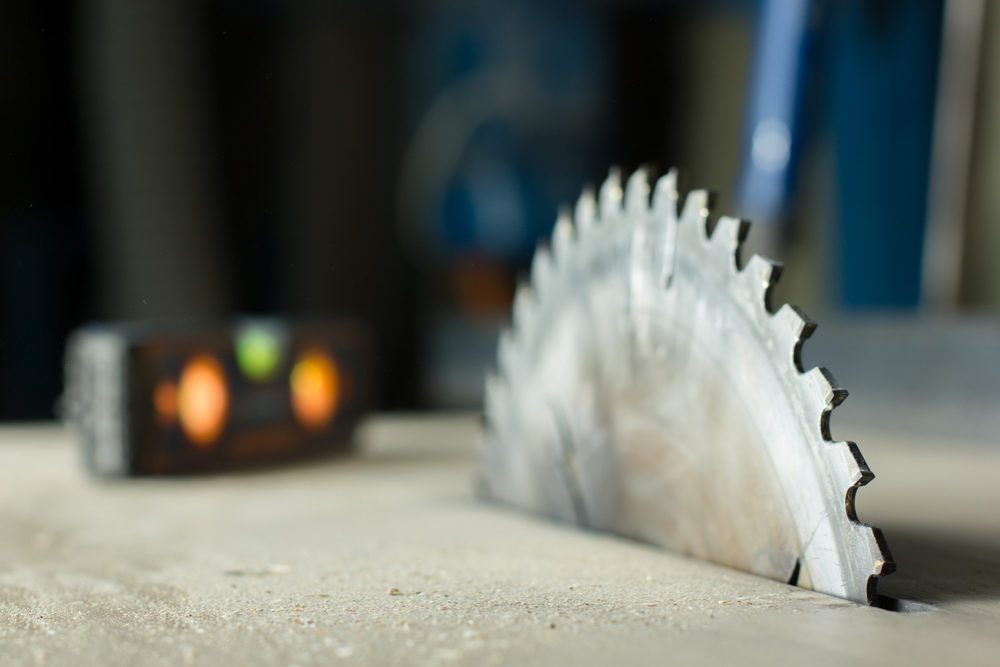
The manufacturer of a table saw has agreed to settle a lawsuit filed by a man left with severe injuries to his hand, which alleges the company failed to include readily available safety features on the table saw, which could have prevented the injury.
The table saw settlement came in a lawsuit filed by Alex Mai in the Philadelphia Court of Common Pleas, against One World Technologies, who manufactured a Ryobi table saw that injured several of his fingers in March 2012. The lawsuit also included claims against the owner of the table saw, Eric Aponte.
According to a report by The Legal Intelligencer, the makers of the Ryobi table saw agreed to pay $1.9 million, and the Aponte agreed to pay $100,000 to resolve the lawsuit.
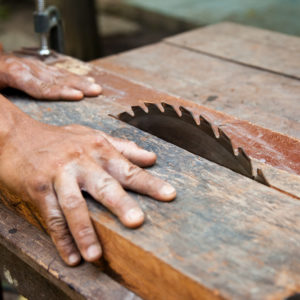
Learn More About
Safety Features Missing From Many Table Saws May Have Prevented Serious Injuries and Amputations.
Learn More About this Lawsuit SEE IF YOU QUALIFY FOR COMPENSATIONMai suffered a severed middle finger and permanent nerve damage to his right index finger while helping Aponte install a hardwood floor. The table saw injury allegedly occurred when a piece of wood connected with the back of the saw blade, resulting in what is known as a “kickback.”
The lawsuit claimed that Mai’s injuries could have been avoided if the Ryobi BTS-10 table saw had come with “SawStop” or another flesh-sensing technology, which would have shut the blade down the moment it contacted with Mai’s skin, resulting in little worse than a nick. One World Technologies failed to install the available safety feature on their table saw, which it agreed to do so as far back as 2002, despite warnings from the U.S. Consumer Product Safety Commission (CPSC) and other safety experts. The lawsuit also claimed the table saw had an ineffective guard design.
The case is one of a growing number of table saw injury lawsuits filed in recent years against several manufacturers over failure to include SawStop Technology, which has been proven to prevent the blade from causing more than a small nick in the skin.
Lawsuits allege that the 20 year-old Saw Stop Technology could prevent most amputations, nerve damage and other injuries reported each year if the safety feature had been adopted by the industry. However, manufacturers have been accused of engaging in a group boycott and refused the license the technology for their products.
SawStop involves the use of a sensor system similar to what is found in touch lamps, which detects electrical conductivity of the human body in proximity to the blade. At the slightest touch of human flesh, the blade is instantly grinded to a stop.
According to a 2014 survey analysis by the U.S. Consumer Products Safety Commission (CPSC), there are about 76,100 table saw injuries annually, based on 2007 and 2008 numbers. The injuries cost a total of about $2.36 billion per year, and leave about 3,000 people a year have with an amputated finger.
The CPSC has been investigating the possibility of requiring new table saw safety regulations, and voted unanimously in 2011 to look at potential new safety requirements. SawStop technology is one of the most likely features to be considered by federal regulators as a standard that should be on every table saw.
Get more articles like this sent directly to your inbox.
"*" indicates required fields
1 Comments
AnthonyMay 21, 2021 at 2:35 pm
Consumer grade saws are all faulty in design. They use blades which are too large in diameter for the motor torque. Constant smoothe operation cannot be maintained while feeding work into the blade. Resulting in chatter, rpm fluctuations causing electrical load fluctuations harmonizing w increased feed loads of same frequency. As the rpm slows gradually while gradually increased feed rate from the[Show More]Consumer grade saws are all faulty in design. They use blades which are too large in diameter for the motor torque. Constant smoothe operation cannot be maintained while feeding work into the blade. Resulting in chatter, rpm fluctuations causing electrical load fluctuations harmonizing w increased feed loads of same frequency. As the rpm slows gradually while gradually increased feed rate from the work bouncing back from the feed hand, the cut is no longer clen as in the cutting path is no longer continuously uniform. There is a pressure buildup of cut material against a deepening cutting path during this inertia transfer, pushing material against the feed hand rather than pulling it away. This intermittent stall increases until kickback in evadably occurs. The light weight of the machine and mechanism play flex and movements allows the machine to dance. Using a table too small to place hands a safe distance from the blade is a further obvious design defect. All in all if you see a table saw with a blade larger than 6" plugging into a 110v wall outlet, don't even look at it. Being opposite the business end of a 7 1/2" blade on a 110 cord is a different story. There is no voodoo magic which can allow the design of a good table saw with a blade larger than 6" not plugged into a 220v outlet. The saw in shop class was plugged into a 45A breaker, it had a 7 1/4 HP motor, it weighed as much as a car, it had a 4' x 5' table. It cut safely, smoothly and effortlessly any fairly dry wood you feed it, it had a 10" blade no guards.